ClevNews
CLEVLINE
WHAT IS THE DIFFERENCE BETWEEN A CONVENTIONAL PRODUCTION PROCESS AND A FULLY AUTOMATED ONE?
In a world where efficiency and quality are essential in any production process, automation is presented as a solution that not only improves processes, but also redefines the way in which they are conceived and executed.
At ClevLine, we have always been committed to innovation and technology in order to offer our customers highly flexible solutions that allow them to remain competitive over time. Thanks to these values and after years of study and development, we have provided the market with a totally innovative concept in the mattress industry: A fully automatic production line for quilted panels, covers and borders, which also combines the functionality of a multi-needle and a single/double-needle in the same machine, being able to work with a multitude of framed, centred, tack & jump and continuous designs.
In this publication, we will explore in detail how our automatic production line has come to revolutionise the way you manufacture your mattresses, offering advantages that go far beyond efficiency.
The Conventional Process: A Sequence of Workstations
Let’s first talk about what a conventional production process is like. As you all know, the panel production process starts with the preparation of the rolls of raw material, passing through the different quilting, cutting and hemming stations, ending with the palletisation of the finished panels. Afterwards, these panels are transferred to the assembly section, where they will be used for the top and bottom of the mattress.
But how is this production process usually carried out? It depends on how the production plant is organised and the type of machinery available. Therefore, based on our experience with different customers, you will find below the process faithfully represented by a series of graphics:
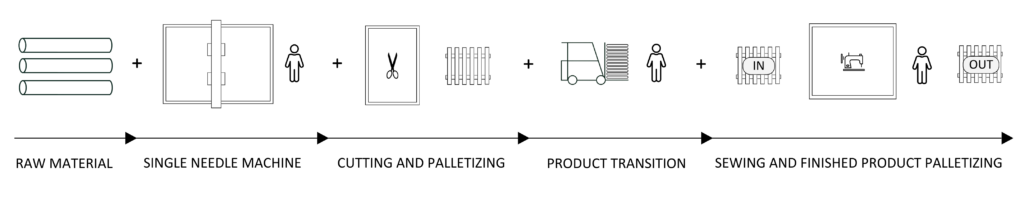
The Automatic Revolution: Integration and Efficiency
Having seen a fairly common conventional production process nowadays, with the number of stations and operators that usually make it up, let us introduce you to how we approach this production process with our CLEVLINE automatic line.
As in the previous case, we start from the raw material rolls to the palletising of the finished product, with the great difference of not requiring any intermediate handling of the product and including all the quilting processes in the same workstation, where only one operator is needed to supervise and control the entire line.
CLEVLINE has a modular architecture, composed of three independent modules that work together for a common purpose:
CLEVONE: Vertical quilting module with four independent sewing heads, qualified to work with all types of designs and a wide variety of materials and thicknesses, guaranteeing a quality finish on each panel.
CLEVPANEL: Automatic hemming module to finish the perimeter of the panel, with high precision in the measurement, reducing the number of workstations and facilitating the subsequent closing of the mattress.
CLEVSTACKER: Automatic stacking module for a higher level of autonomy in the process, eliminating repetitive tasks of low value for the operator.
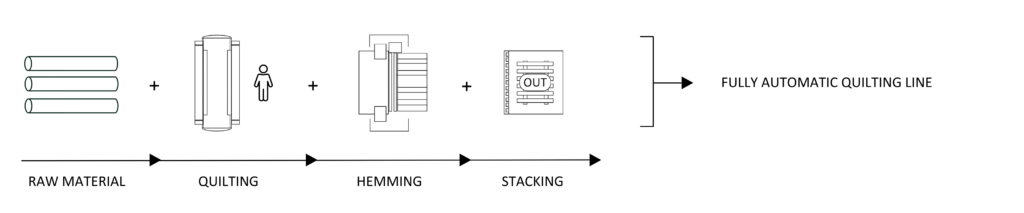
Competitive Advantages:
In addition to improving the production process and the quality of the end product, our automatic line offers a host of unrivalled benefits:
1
Increased Efficiency: With a continuous and uninterrupted work sequence, downtime is minimised, resource utilisation is optimised and, as a result, overall process efficiency is increased.
2
Reduced Costs: By eliminating manual handling of products at different stages of the process, labour and production costs are significantly reduced.
3
Space Optimisation: By integrating all processes into a single workstation, the need for additional space and machinery is reduced, leading to considerable savings in floor space.
4
Improved Product Quality: The automation of processes reduces the risk of damage and flaws during the manufacturing process, ensuring greater consistency in the quality of the final product.
5
Flexibility and Adaptability: Our line allows quick and precise adjustments according to specific production needs, combining the functionality of a multi-needle and single/double-needle in the same machine.
6
Greater Process Control: Automation allows greater control and supervision of the production process, as all parameters and variables can be monitored and adjusted in real time.
7
Operator Care: It frees the operator from repetitive and routine tasks, allowing them to focus on higher value activities such as production process supervision, quality control and problem solving, providing them with greater job satisfaction.