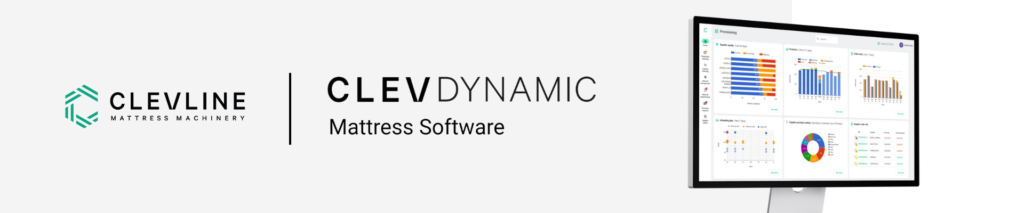
What does it take to digitize your mattress manufacturing plant?
The era of Industry 4.0 is headed by a concept that many people are unfamiliar with or confused about; digitization.
Broadly speaking, it is based on the use of digital technologies to change a business model and provide new opportunities and ways to produce revenue and value.
Today, it has become a requirement to maintain and boost competitiveness in an increasingly automated industry; an essential to not fall behind in the market and to acquire a wide range of advantages for your mattress production plant and the rest of the company.
Another aspect that often creates discrepancy among many users is the false belief that it is a change that needs to be implemented in a radical way, but nothing could be further from the truth. At ClevLine we always support the theory that it can and should be implemented progressively, as it completely transforms the way in which companies operate and make decisions.
Why make this change?
Making the decision to digitize your mattress factory is also often seen as a difficult challenge to tackle, as it seems to involve multiple implications and significant changes.
As a company, we are often looking for comfort and wellbeing, which prevents us from seeing the advantages of leaving our comfort zone. And the fact is that digitalisation represents a big change, yes, quite a big change, but it is about implementing a new way of doing things, to take the leap to a higher level, as far as management is concerned.
On the other hand, the concept of digitalisation and automation has always been accompanied by the fear of replacing and substituting the human team, but the challenge lies in convincing the production team that, far from being replaced by technology, it will free them from monotonous tasks and allow them to work more efficiently and feel more productive, thanks to being able to take charge of functions that add value to the company.
As mentioned before, the digitisation of a mattress manufacturing plant is not an easy process, as it involves multiple factors, so it is crucial to map it out properly in order to achieve lasting success. Ideally, changes should be implemented gradually, avoiding changing the way of working completely from the very beginning.
How is it done and what does it entail?
We would like to start this brief explanation with a concept that you may be familiar with: The Internet of Things (IoT). Basically it is about connecting physical elements to the Internet, in this case, to our ClevDynamic system.
Our way of doing this is through the monitoring of the factory’s equipment in order to collect data in real time, which, in turn, almost instantaneously, is reflected and presented in a graphical and representative way for the person in charge, with the aim of providing and facilitating decision making. We do not want to create a huge flow of numerical data that the user must take to other external applications or be forced to generate their own Excel pivot tables to obtain information from a huge amount of data.
The control and analysis of the data collected during manufacturing is reflected through an easy-to-interpret interface that allows faults, anomalies and incidents in the process to be detected, so that rapid action can be taken and predictions can be made about future situations.
ClevDynamic creates a digital model of the manufacturing process of each product, bringing together all the information about its characteristics, materials and procedures from its technical data sheet in a single place.
At the end of the day, it is a tool that allows the optimisation of industrial production processes, enabling the reduction of delivery and supply times, and significant cost savings and inventory optimisation.
If you would like to learn more about digitalisation and how it can benefit your company, contact us now! We will be happy to help you make the leap to Industry 4.0.